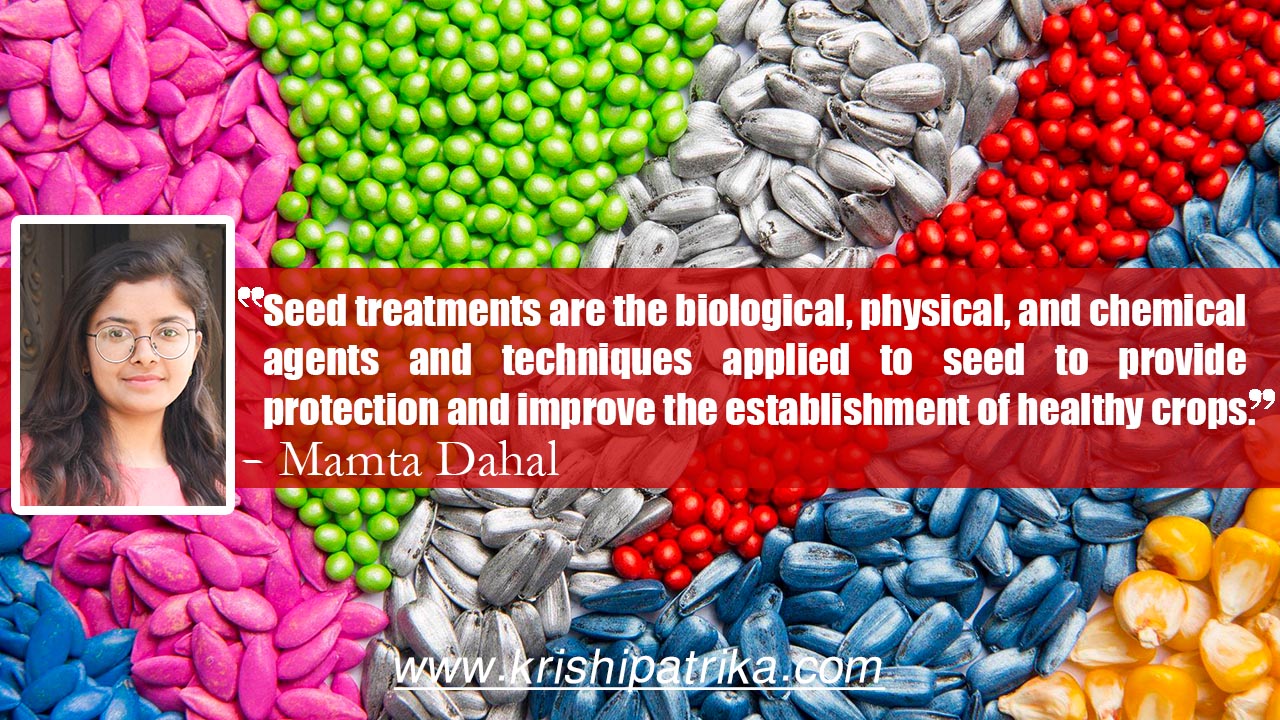
Seed treatments are the biological, physical, and chemical agents and techniques applied to seed to provide protection and improve the establishment of healthy crops. It also refers to the application of fungicide, insecticide, or a combination of both, to seeds so as to disinfect and disinfect them from seed-borne or soil-borne pathogenic organisms and storage insects.
Advantage of seed treatment:
- Early-season protection against pathogens
- Early-season protection against insect pests
- Improves germination
- A healthy start
- A safer application
- More consistent stands and better yields
- Protection from seed rot and seedling blight
- Help in breaking dormancy
- Help in inducing drought tolerance of crop
Disadvantages of seed treatment
- Limited protection under high pest pressure. Under high pest pressure, significant crop damage may occur.
- Duration of protection.
- Limited shelf life of the treated seed.
- Phytotoxicity.
Methods of seed treatment:
- Seed dressing: Seed dressing is the process of treating seed with antifungal and antimicrobial chemicals prior to sowing. The seed is dressed with either a dry formulation or wet treated with a slurry or liquid formulation. Dressings can be applied at both farms and industries.
- Seed coating: Seed coating is the application of materials onto the surface of seeds for the purpose of making seeds’ shape, size, weight, and seed surface more uniform to make them easier to plant and/or to apply active compounds that improve seed quality and protect the seed from biotic and abiotic stress. A binder is used with a formulation to enhance adherence to the seed. The coating requires advanced treatment technology, by the industry.
- Seed pelleting: Seed pelleting is the process of adding inert materials to seeds increasing their weight, size, and shape. This improves plantability allowing for precise metering, spacing, and depth of seed in the field.
Under the following conditions under which seed must be treated:
- Injured seeds: Injured seeds or break seed coats may afford an excellent opportunity for fungi or bacteria to enter the seed for killing embryos or weakening the seedlings that will be produced from it. Seeds suffer a mechanical injury during combining and threshing operations or from being dropped from excessive heights or may be injured by weather or improper storage.
- Diseased seed: Disease organisms can infect the seeds during harvesting or processing time. If the seed is processed on contaminated machinery or if stored in contaminated containers or storehouses the contamination chances will be high.
- Undesirable soil conditions: If the seeds are planted under unfavorable soil conditions such as cold and damp soil or extremely dry soils, which may be favorable for the growth and development of certain fungal spores to attack and damage the seeds.
Chemicals used
1. Mercurials:
- Organo-mercurials: Recommended for the treatment of small grains, flax, cotton, and safflower; example: Agrosan GN, Ceresan
- Inorganic mercurials: eg. Mercuric oxide, Mercuric chloride, Mercurous chloride, etc.; limited primarily to seeds, roots, tubers, garden and vegetable crops
2. Non- mercurials:
- Organo non-mercurials: eg. Thiram, captan, etc.; used for millet, maize, wheat, barley; act as seed disinfectants and/or seed protectants
- inorganic non-mercurials: eg. Copper sulfate, Cuprous oxide, Copper carbonate, etc.; used for wheat
Methods of seed treatment:
- Dust Treatment: Seeds are treated with dust fungicides in a closed barrel-type rotating drum, usually applied at rates of 200 to 250 grams per quintal of seed.
- Wet treatment: Water-soluble chemicals are dissolved in water in containers and seeds are dipped for a certain period of time and then dried properly before packing and storing
- Slurry treatment: Chemicals are mixed with a small quantity of water to make a slurry and then the mixture is applied to seeds in automatic or semi-automatic machines.
Seed treatment equipment:
Commercial seed treaters are designed to apply accurately measured quantities of pesticides to a given weight of seed. Basically, there are three types of commercial seed treaters on the market: dust treaters, slurry treaters, and direct treaters-the Panogen and Mist-O-Matic treaters are examples of direct treaters.
1. Dust Treater (Gustafson XL Dry Powder Seed Treater)
Controlling the flow of Seed: the amount of seed that flows into the weigh pan (which is just beneath the feed hopper on top of the treater) is controlled by opening or closing the gates of the feed hopper by means of the handwheel on the side of the hopper. The scale on the hopper shows how far the gates are open (in inches). Gates should be open to whatever number of inches it takes to keep the weight pan filled to the required number of pounds per dump as it tilts in either direction. The number of pounds per dump is adjusted by correctly setting the counterweight up or down on the counterweight arm.
2. Slurry Seed Treater
The slurry treatment principle involves the suspension of wettable powder treatment material in water. The treatment material applied as a slurry is accurately metered through a simple mechanism composed of a slurry cup and seed dump pan. The cup introduces a given amount of slurry with each dump of seed into a mixing chamber where they are blended. While the operation of the slurry treater is relatively simple, the various operation procedures must be thoroughly understood
3. Panogen Seed treater
The operation of the Panogen treater is relatively simple. A small treatment cup, operating from a rocker arm directly off the seed dump pan and out of a small reservoir, meters one cup of treatment with each dump of the seed pan. Fungicide flows through a tube to the head of the revolving drum seed mixing chamber. It flows in with seed from the dumping pan and is distributed over the seed by the rubbing action of the seed passing through the revolving drum. The desired treating rate is obtained by the size of the treatment cup and by adjusting the seed dump weight. Treatment cup sizes are designated by treating rate in ounces and not by actual size-e.g., the ¾ ounce cup applies ¾ ounce (22.5 ccs) of treatment per bushel with six dumps per bushel. The actual size of this cup is approximately 3.75cc.
4. Mist-O-Matic Seed Treater:
The “mist-o-matic” treater applies treatment as a mist directly to the seed. The metering operation of the treatment cups and seed dump is similar to that of the “Panogen” treater. CUp sizes are designated by the number of cc’s they actually deliver-e.g., 2 ½, 5, 10, 20, and 40. The treater is equipped with a large treatment tank, a pump, and a return that maintains the level in the small reservoir from which the treatment cups are fed. After metering, the treatment material flows to a rapidly revolving, fluted disc mounted under a seed-spreading cone. The disc breaks droplets of the treatment solution into a fine mist and sprays it outward to coat seed falling over the cone through the treating chamber. Just below the seed dump is two adjustable retarders designed to give a continuous flow of seed over the cone between seed dumps. This is important since there is a continuous misting of material from the revolving disc. The desired treating rate is obtained through the selection of treatment cup size and proper adjustment of the seed dump weight.